![]() |
![]() |
![]() |
![]() |
![]() |
You are here: Home » Specialized Sections |
![]() |

FAQs (Frequently Asked Questions)
See also:
Q: "Decimation", "Reduction", "Simplification". Are these all the same?
A: Polygon reduction is often referred to in different ways, and "Decimation", "Reduction", "Simplification" are common terms.
Q: What gets removed first from a model?
A: Small polygons and areas of low curvature (flat planes made up of multiple polygons) get removed first.
Q. What is the most optimal method to reduce an object which is to have one continuous surface, but which is really made up of multiple objects, such as an outer car body?
A. Since you probably do not want cracks to appear between abutting car body panels, the ideal method is to move all objects that make up the car body into a single object, apply the polygon reduction algorithm, and then optionally explode the reduced mesh into separate objects again (the latter is only possible if the various objects originally had different materials assigned to them). This series of operations is explained in the Polygon reduction tutorials.
Q: Holes are appearing in my final model. Why? Can I fix them?
A: You might say that the holes were in the original model to start with. Take for example two abutting mesh surfaces with a common curved edge; it just so happens in this example that on one side of the surface there are many more vertices which make up the curved edge than on the other edge. Because there is no common vertices between the two mesh surfaces they will be reduced differently irrespective of the curvature of the other surface. Thus, more vertices may be deleted from one edge than the other, thus leading to "cracks" that will appear between the previously abutting mesh surfaces. One way to ensure two abutting surfaces remain "glued" together is to have the common edge share the same number and location of vertices. The second more realistic and hands-on method is to increase the "Boundary preservation weight" type-in value shown on the "Weightings" panel or enable the "Lock the vertex positions of vertices on mesh borders" checkbox on the same panel. These latter two options will prevent boundary vertices from moving greatly, thus leading to less cracking between adjoining models.
Q: Why does the model get skewed or twisted badly if I use a high level of reduction (90%+) and enable the "Lock the vertex positions of vertices on mesh borders" checkbox?
A: This is because the boundary of the mesh is not allowed to be changed so there is too few degrees of freedom for the polygon reduction algorithm to adequately reduce the model uniformly and still achieve the desired level of polygon reduction. Rather than having some preference go to the boundary vertices for reduction/movement, all reduction/movement must be done with non-boundary vertices which leads to extreme movement of interior vertices. To fix this problem, reduce the amount of polygon reduction wanted or disable the "Lock the vertex positions of vertices on mesh borders" checkbox and use the "Boundary preservation weight" type-in value instead.
Q: Material attributes might look vastly different after polygon reduction. How can I prevent these visual changes from occurring?
A: These are termed "Material Attributes" in the polygon reduction algorithm. The basic job of the reduction algorithm is to remove vertices in order to collapse polygons into fewer numbers of polygons. However, this often leads to less visually pleasing results since material attributes are not taken into account during the reduction process. To increase the importance of these attributes, increase the "Material preservation weight" type-in value shown on the "Weightings" panel or enable the "Lock the vertex positions bordering two materials" checkbox on the same panel. The latter checkbox will prevent vertices from moving at all if they have different material characteristics on either polygon to be collapsed.
Q: I had 100 normals and 20 uv tangents in my original model, but the simplified model contains 234 normals and 234 uv tangents. Why? Can I fix it?
A: In such cases the uv tangents are usually the culprit. Unlike most other attributes which are usually shared nicely by all polygons at each vertex, such as normals, uv tangents may be shared badly, creating too much replication. Try unchecking the "Retain UV tangents" option if those are not important to you.
Q: Why does my model look very bad after simplification, no matter how much I try to tweak the various options? Is there any way to get good results from a model like this?
A: It is likely that the original mesh has a messy polygonal topology, which wreaks havoc on the reduction algorithm. The ideal mesh for reduction is one that is well connected and its properties are well shared. The way to test this is to inspect the polygon information of a mesh. If a triangular mesh has N number of vertices, it should have about 2N polygons (1N for a quad mesh) and not much more than N number of any attribute. If there are much less than 2N polygons, that means the polygons are not well connected and many vertices are not shared well. There are too many boundary edges which require too many constraints, and the object can't really be kept coherent. If there is much more than N number of any particular attribute, that means that property is not shared well at all the vertices, therefore a lot of material boundary constraints will be inserted at the discontinuities, which can distort the reduced geometry. An effective solution in these cases is to run some polygon processing routines on the mesh before, and possibly even after reduction. Simply using the default options of the indexed polygons manipulation function dialog box will usually work well.
Q: Why does my model only reduce by 65% even though I specify 80%?
A: The "Geometric Error Tolerance " error bound is probably too low for your particular model.
Q: How can I apply polygon reduction in a batch fashion to all 3D files I have in one directory?
A: You can apply polygon reduction during the Batch 3D Conversion process by enabling the "Perform Polygon Reduction on Each Model" option on the batch 3D conversion options dialog box.
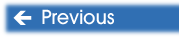

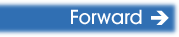